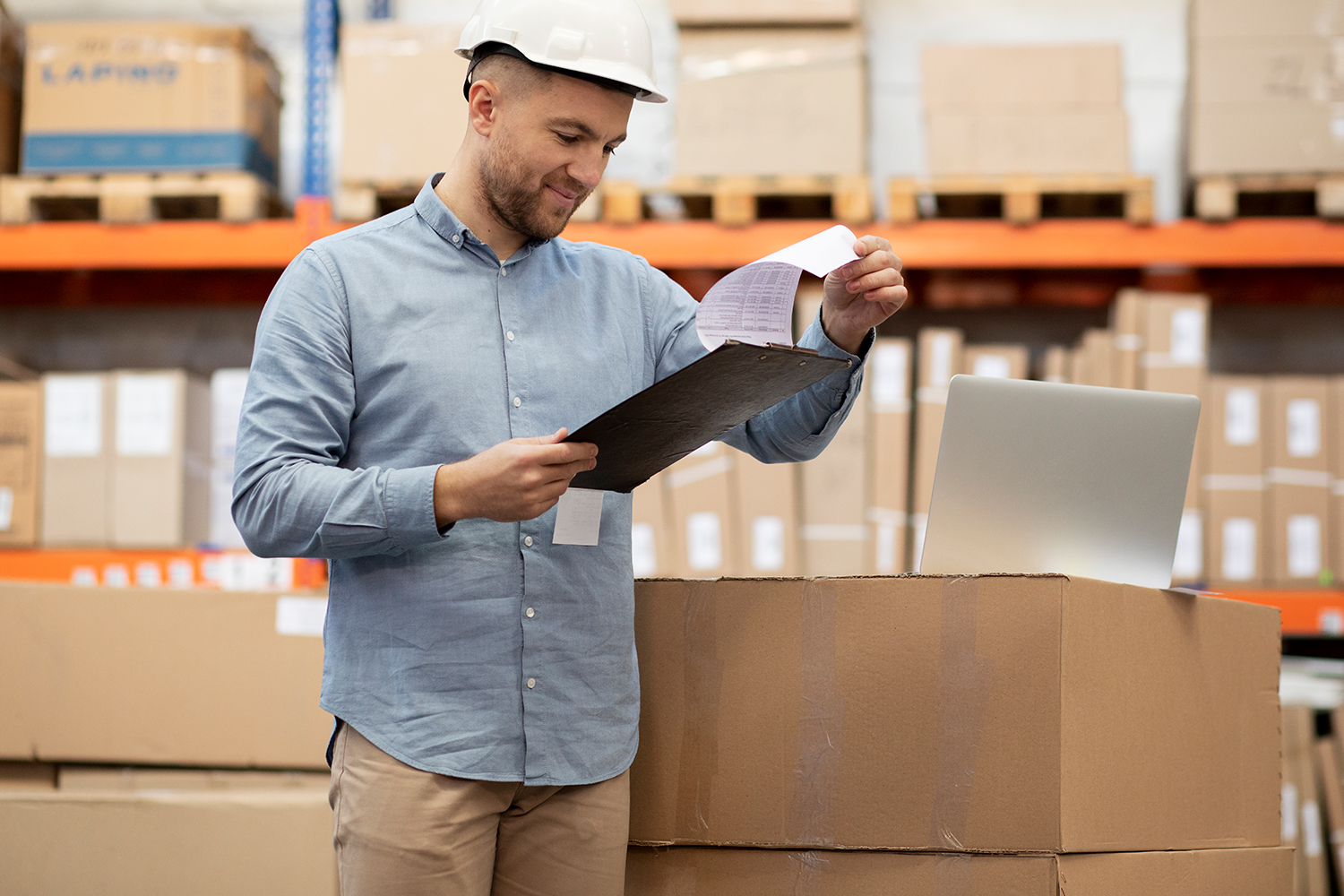
Why having an inventory in your business
Keeping an inventory, as well as controlling it, is a key part in the administration of a business, however, it is rarely taken care of correctly due to different circumstances, but the main factor is that small businesses do not give it the necessary importance, which many times leads to failures in the management of the companies.
The word inventory is perhaps a word that you have heard many times, even if you do not manage a company or you are new to entrepreneurship. Maybe you have heard it so much by now that you think you understand it, although you have never used it in your daily life; therefore, in order for you to understand it more clearly, we will talk about the importance of having it and keeping it correctly.
What is an inventory?
The first thing we need to explain before talking about inventories is what they are. We can say that an inventory is the storage of material goods for a period of time, which help you to sell your product or service at present or are there to do so in the future.
On the other hand, the Royal Spanish Academy defines inventory as "An entry of goods and other things belonging to a person or community, made with order and precision". So it includes not only the storage, it also includes the ordering of those goods, so it is understood that an inventory can be the storage, the ordering or the combination of both.
It is necessary to have products stored and properly ordered to keep your business running, as well as to prevent properly, which will allow you to continue offering a quality service over time, but otherwise you will eventually fail your customers and suppliers.
What is an inventory for?
You may be asking what is the purpose of accumulating and ordering all your goods. Basically, the answer is to improve two essential processes in all businesses: the supply of your raw materials and adequately cover the demand with the products or services offered by your business.
For supplying, with an inventory you can be prepared to order supplies that you need in time. In terms of meeting demand, it is your finished product inventory that allows you to know how much of each product you have so you can be ready and prepare more before your products run out.
When you have an inventory, you can plan better because it will give you a clearer idea of the time you need to order your raw materials, as well as how many products you need to create to cover the demand, since experience teaches you to consider external and internal factors.
Although you may not have thought about it, it also serves to improve your customer service, since you will always be ready to meet the demand and your customers will not be disappointed if they arrive at your store and cannot find what they were looking for because you ran out.
One of the advantages of having an inventory is that it helps you to prevent fluctuations in market prices, thus finding lower prices at a given moment will allow you to acquire them and keep them in stock, before they start to increase their costs. Be aware that for this to work, finance managers must be involved and evaluate if it is a good time to buy more than you need.
Which businesses may have inventory?
Essentially, no matter what you sell or offer in your business, any company needs to keep control of the products it sells in order to avoid shoplifting, items shrinkage or waste that could seriously affect the profitability of your business.
Whether you belong to the manufacturing, service, distribution, sales, beauty, restaurant or any other sector, an inventory can be used to improve your management, correct your processes and prevent any situation.
The best thing to do is to adapt it to your type of business, way of working and line of business, because from a tacos restaurant to a small shop you can implement it, yet it works differently for each one, so here we explain how to carry out an inventory and the most common ways to do it.
How should I conduct an inventory?
Knowing a bit more about what inventories are and their purpose, now is the time to create one, but not just any one, you have to know that there are different types and their classification depends on the type of industry or business you have, and how you arrange your products, therefore, it is necessary to explain the simplest ways to create an inventory..
Inventories according to time
This may include the initial inventory, which is nothing more than the inputs you have before you acquire more or sell the one you currently have.
Secondly, the final inventory, which is the stock count of your inputs at the end of a defined period, which is usually an accounting period, and serves to determine your equity situation; that is, it is established on paper what you did not sell or transform.
Inventories according to logistics
With this classification, the operation and the logistics area are considered, so batch inventories are those that are operated according to a batch, that is to say, a determined quantity of items that are received or produced on a determined date. Batch inventories reduce costs by supplying in large quantities.
Seasonal inventories are another type of inventory, they are designed to meet the demand of the moment and are used to satisfy the seasonal demand, such as the Day of the Dead or Christmas.
Safety or buffer inventories are part of the inventories according to logistics and exist to cover the uncertainty in the demand or supply of items. Safety inventories are named as such because they are a kind of buffer in case of a slight crisis, such as a supplier's strike or a vacation.
Inventories according to periodicity
Perpetual inventory is a type of time-dependent inventory, which allows you to know at any time the value of the final inventory without the need to carry out physical inventories.
Accounting allows you to discover losses, thefts or errors in the handling of merchandise, since you know the exact value of the inputs that should be there. These inventories enable you to keep your store always open because it is not necessary to close it to do a count, as it is always monitored.
Besides, other type of inventory carried out by periodicity, is the periodic inventory in which specific dates are established so you can count all your supplies or merchandise, this is when we commonly see a business that says: Closed for inventories, because it takes a lot of time and effort to be carried out..
Inventories by shape
When it comes to production systems, such as a bakery, carpentry and others requiring raw materials to be transformed, the simplest way to classify them is through the value added during the manufacturing process. In other words, they are classified into raw material, product in process and finished product.
Raw material is understood as any material needed to create a new product, such as screws, glue or flour; in the case of in-process product, it can be inventory that is waiting to be processed or assembled, or that is in a rough assembly that needs details to go on sale.
Finished products are the final product of the production process and are available for sale to the general public. Though it can also be a product that is not precisely for sale, but necessary to assemble something else, for example, a lumber company that cuts trees and at the end produces boards or paper needed to assemble furniture or create notebooks.
When talking about an inventory in a production process line, usually they mean the storage of material in which the manufacturing is located.
Although these are not all the inventories that exist, they are the most common ones, so you could check which of them can be adapted to your business or the way you can implement them to obtain great results when it comes to your business management.
Inventory organization
Previously we described how we can classify inventories, often related to the moment you are living, but also to the line of business of your company or business, so with this in mind, now we will tell you the most common ways to organize an inventory.
ABC method
This is the most common method because it helps you classify your goods based on how valuable they may be and not on the volume they occupy or the quantity of them. This way you can identify the most valuable items to record them correctly and have an overview of the important and unimportant items.
The importance order will depend on your business line; for example, being a bakery, the most important thing is not the bread made, it is your raw material that could expire at any time and become waste. But for a factory, your most valuable material is your finished product because that is what you sell to the public and what makes the most profit.
Then, you will classify the items under this method by giving them a letter from A to C, to classify them from most to least important, as we said, the importance will depend on your line of business, here we help you to understand it better.
A items are those where your company has its largest investment and usually represent 20% of the inventory cost. They are the most expensive; but as we also mentioned, they can be the most critical in terms of the use that is required or the purpose for which they are going to be used within the company.
B items represent the next level and represent approximately 30% of the inventories. This percentage can vary, it is not fixed, but is an example to clarify the case.
Lastly, C items are those that have a higher volume or we have them in greater quantity and represent 50% of all the items we have in the inventory. It is the smallest investment.
Besides the fact that it helps to put more emphasis on certain products, this classification allows you to determine in a visual way which are the items you have to pay more attention to, since they are within sight, they are not so hidden and you will always find them when you go to the warehouse.
First In First Out (FIFO) method
The name of this method explains it all: everything that arrives first in the warehouse is the first to go. So you will not have to worry about your products expiring or going down in price and still have them at a very high cost.
It has a clear record of the entry of each product and the quantities of the same, as well as the sale at the time so that it is recorded in the warehouse. This way you can constantly renew the warehouse when needed. With this method you can also decide that you will not acquire that input again because it was not sold and make a decision immediately.
This type of method has the advantage that you don't need a large warehouse because it will only be there for a short time. So whatever you have for retail and a little in stock will cover your demand and you can order it immediately when you do not have it. Maybe one of the scenarios where it works best is in a small store.
Last In First Out (LIFO) Method
You may have guessed it, this method implies that the goods last added to inventory will be the first to be removed from inventory for sale. While it may seem odd, or unnatural, there are companies that have to use this method to manage their inventory.
Homogeneous raw material product sellers working with bulk inventories, such as stone, sand and bricks. Usually and for handling and logistical reasons, they have to inventory the top of large piles or stacks, leaving the older lots at the bottom of the stacks for much longer.
For example, you have a vending machine and companies such as vending machine operators also have to choose LIFO for inventory management, since the first products they put into their machines are the last ones to be sold.
Cyclic counting method
In this method, you simply count your products on a specific date. Products to be matched will be previously selected and many times they will be determined by being the most expensive, important, expensive or hard to get.
You can combine this method with other methods, as it will allow you to decide which type of product is relevant or allows you to match one to another to generate accurate counts, which will allow you to detect discrepancies in inventories and identify the reasons for them.
The inventory is an expense or an investment?
This article has already covered what an inventory is and how you can have one, how it helps you in your day-to-day business and how it can help your business. But it is important for you to know that inventory control is indispensable for every organization.
Literature indicates that a typical manufacturing company keeps approximately 20% of its production as inventory, and has an annual cost of holding inventory of about 25% of its value. In other words, 20% of their production is in the warehouse and it costs them 25% to keep it there.
Without proper inventory control, the costs could be excessive for your business, which will cause your capacity to shrink and not be able to compete with the market.
An efficient inventory control determines the long term life of the company.
A major concern for any company is reducing the costs of having an inventory, but the problem is not only to reduce the stock of products, but also to establish the right strategy to manage and control that inventory.
What is the cost of an inventory?
While it is correct that an inventory will cost you money, people and time, you will always see it as a necessary investment. An inventory will allow you to ensure the continuity of your production and consequently deliver a great service to your customers.
It is possible to determine four types of costs for inventory management. Identifying them is very important in order to control them and not see them as a burden on your business.
Setup costs
Here you can basically identify costs that are generated when issuing a production or purchase order. In other words, how much it costs you to generate the order, preparing it, tracking it, processing the invoices or plant reports and preparing the payment. Here you should also include the cost of installing the equipment necessary to generate your products or perform your services.
Maintenance costs
To have a product in storage costs you money; that is why it is necessary that your inventory is constantly in rotation and does not last long in storage. Here costs for investment, deterioration, obsolescence, insurance, taxes, etc. are included. Also, they cost you handling, security, space and record keeping requirements. Now you see the importance of your inventory turnover.
Shortage costs
Suppose that one of your products is requested by your customers and you do not have it or do not have enough of it. That represents a loss of money and even worse, that your customers do not trust your service because of the shortage of a product.
Same thing happens with the lack of raw material, not being able to produce your product or not with the same quality will result in the loss of sales and even customers. For this reason, it is important to have an inventory, which will allow you to avoid shortages of raw materials.
Capacity-related costs
Just imagine that you decide to increase your inventory because your orders are growing, you will have to rent a bigger warehouse and consequently, hire a bigger staff. So you will have to think about hiring and training more staff, buying more equipment and preparing for the learning curve.
While inventory management and administration have these costs, it is very important to have them because they will help you to have your products always available, keep control over your sales and better understand your customers during specific times of the year. Having an inventory is not an expense, but a solid investment to enhance and expand your business.
The mistake of not having an inventory
We have seen that the biggest problems associated with not keeping an inventory are the discrepancy between the items you were supposed to have purchased and the items that are actually there, meaning a number of problems:
- Poor manufacturing of your products. If you do not have enough supplies, you will not be reaching your goals, so many of your customers may be dissatisfied and will probably search for someone else to satisfy their demand.
- Management mistakes. The whole planning can fall apart if you don't have an inventory that allows you to understand and prevent enough material to generate your products without exceeding them.
- Material theft. If you do not have all the material you own accounted for, you could be suffering from ant theft from your workers and "customers", because you will not realize when this happens and you will not be able to act immediately.
So important is the issue of theft that the National Association of Supermarkets and Department Stores (ANTAD) reports that ant theft causes around 140 billion pesos in losses every year.
Clip Catalog
You already know more about inventories, the importance of having one and what types exist, it's time to make one in your business and to help you, Clip has a completely free digital catalog.
There you can enter all your products, mark a sale and it automatically deducts from your inventory. In addition, it will allow you to get paid faster and easier, because you can enter directly into the catalog to select the products sold. And you will even be able to charge using your device's camera as if it were a barcode reader.
Catalog Activation
If you did not register any product or you are a new user, simply log in to your Clip App and you will find this option in the Preferences section, activate the Catalog button and you're done. The transaction screen will now display four icons at the top of the screen.
The first one, from left to right, allows you to make a transaction as you normally do; the second one shows the registration of all your products, if you have not registered anything we can show you how to do it.
The third one from left to right enables you to open the camera to perform the transaction by reading the barcode of your product previously registered, and simply scan it, and the last one is a shopping cart that allows you to see the summary of everything you are about to collect.
Product Registration
In order to register all your products you need to go to the Clip application and select the Catalog option, there you will find two menus: products and categories. It will be up to you which one to start with.
In the Products option you can register each of the products or goods you have, you can register them one by one through the app, choose a picture, color or something that identifies them and then write the product name.
Then, enter the retail price and in case it has a barcode and you want to register it, you can click on the icon and it will open the camera for you to register it correctly. Remember to enter the quantity of these products that you have in your inventory.
If you have a Category, this is where you should enter it. For example, if it is a lemon soda, you could add it to the Sodas category. Finally, if there is a specific variant of that product, you can add it, in this case, if you are registering a lemon soda, a variant could be diet. Just repeat the same steps and you are done.
For the Category option the process is similar, simply add a photo or image that identifies them, name them and if you did not have products in this category, you will be able to add them. To do this, you must have registered products and check the box of those that belong to this category. Then click on Confirm and that's it.
So your inventory in the Clip App will be organized by Category, then Product and finally by variant. Each time you make a sale, the product will be automatically deducted from your inventory for you to control and manage everything you sell.
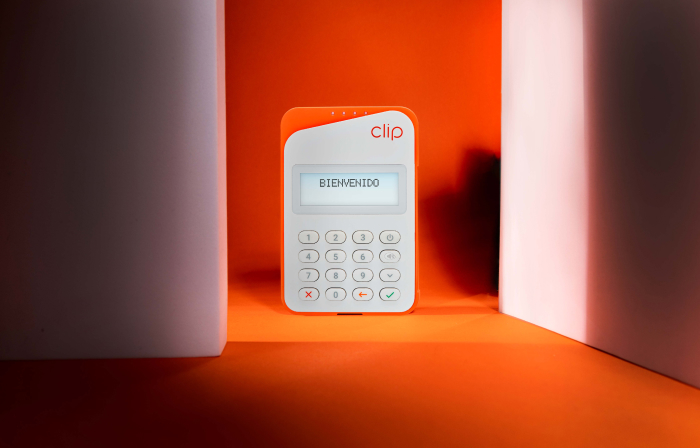
As a leading fintech company, we are frequently under the spot.
Go to Clip in the news*Spanish content only
By clicking Subscribe you're confirming that you agree with our Global Policy.
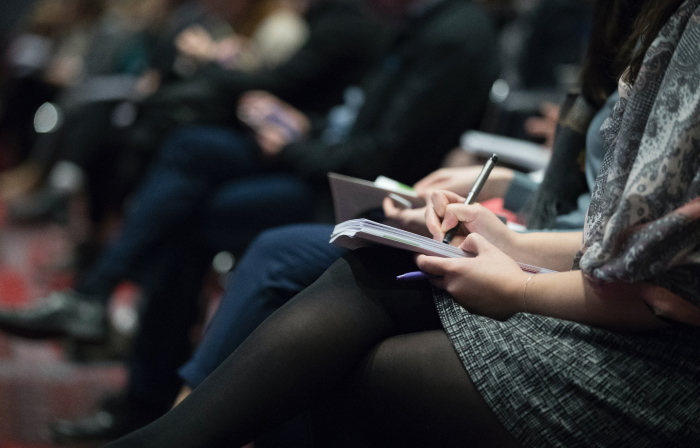
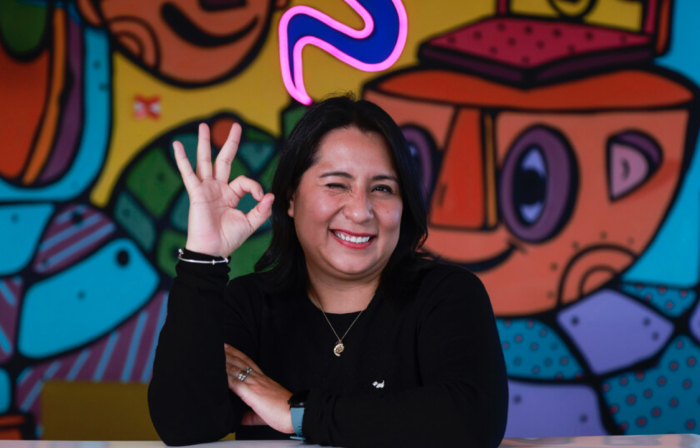
Explore our current positions. Your next job could be around the corner.
Go to careers